Lightweight insulating concrete (LWIC) is a versatile construction material known for its thermal insulation properties and reduced weight compared to traditional concrete. This article explores what LWIC is, its types, applications, benefits, and more.
Table of Contents
Types of Lightweight Insulating Concrete
Lightweight insulating concrete (LWIC) encompasses various types, each designed for specific applications in construction. This article delves into the different types of lightweight insulating concrete, their characteristics, uses, and benefits.
1. Cellular Concrete
Cellular concrete, also known as aerated concrete or foam concrete, is characterized by the inclusion of air voids or bubbles within the concrete mixture. These air voids are typically introduced through the addition of foam or by incorporating lightweight aggregates such as perlite or vermiculite.
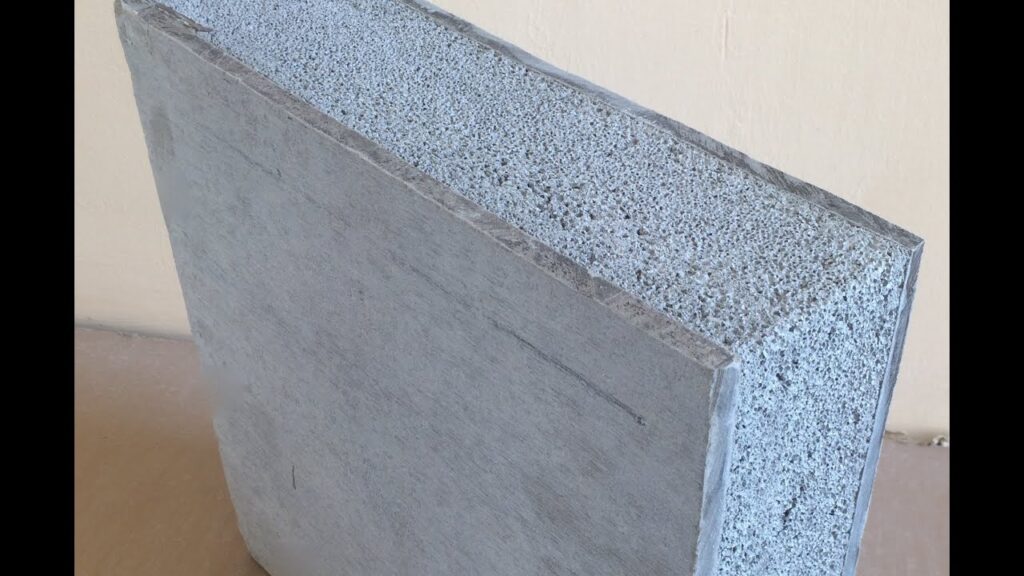
Cellular concrete offers excellent thermal insulation properties and is known for its low density, making it suitable for applications where weight reduction is crucial, such as roof insulation and void filling.
- Properties of Cellular Concrete
- Applications of Cellular Concrete
- Advantages of Cellular Concrete
2. Foam Concrete
Foam concrete is a lightweight concrete variant where foam is added to the cementitious mix to create air bubbles. These bubbles impart insulation properties and reduce the overall weight of the concrete.
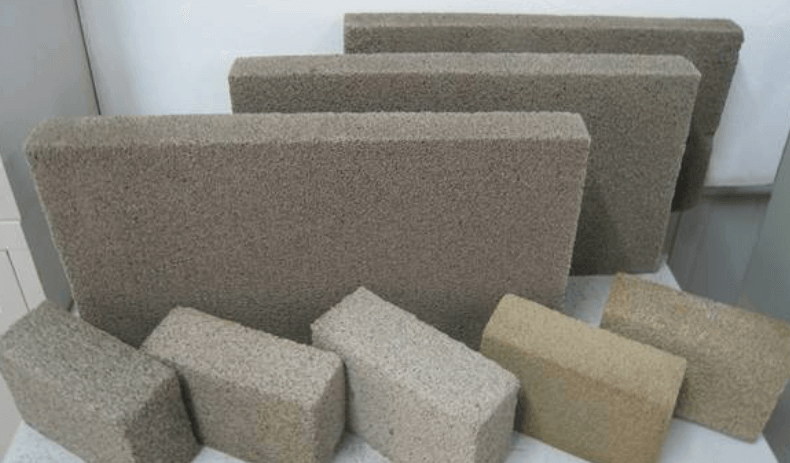
Foam concrete is highly flowable and can be pumped into place, making it ideal for filling cavities, voids, and trenches in construction projects. It is used extensively in ground stabilization, insulation under floors, and lightweight roof screeds.
- Composition of Foam Concrete
- Uses of Foam Concrete
- Benefits of Foam Concrete
3. Perlite Concrete
Perlite concrete incorporates perlite, a volcanic mineral that expands when heated. Perlite aggregates are lightweight and provide excellent thermal insulation. Perlite concrete is commonly used in roof decks, floor fills, and insulating blocks due to its fire-resistant properties and ability to reduce heat transfer through building assemblies.
- Characteristics of Perlite Concrete
- Applications of Perlite Concrete
- Advantages of Perlite Concrete
4. Vermiculite Concrete
Vermiculite concrete utilizes vermiculite, a natural mineral that expands similarly to perlite when heated. Vermiculite aggregates are lightweight, absorbent, and offer good thermal insulation properties. Vermiculite concrete is used in lightweight roof screeds, insulating concrete blocks, and chimney linings due to its ability to withstand high temperatures and provide sound insulation.
- Properties of Vermiculite Concrete
- Uses of Vermiculite Concrete
- Benefits of Vermiculite Concrete
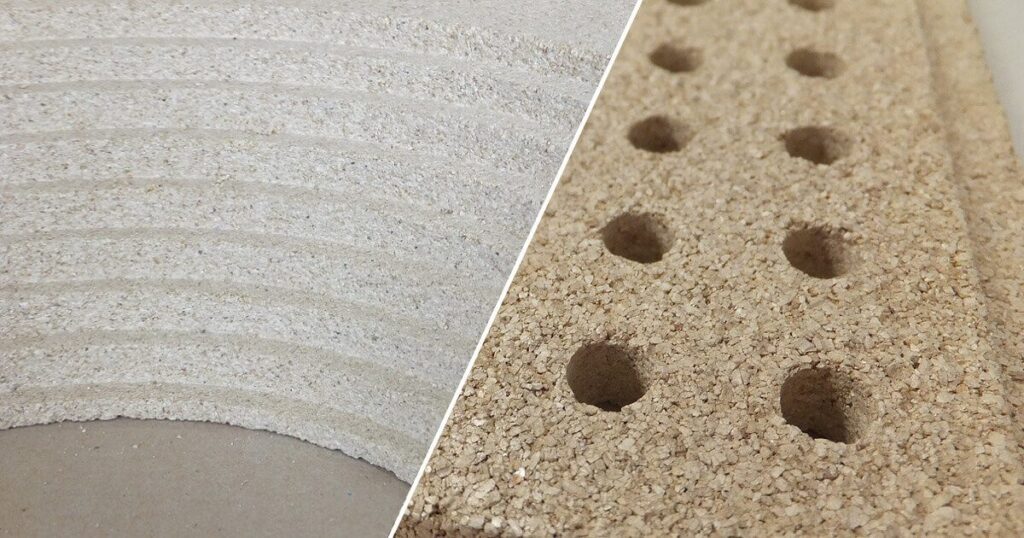
When selecting a type of lightweight insulating concrete for a project, factors such as thermal performance requirements, structural needs, and environmental conditions must be considered. Each type offers unique benefits and is tailored to specific applications in construction, ensuring efficiency, sustainability, and cost-effectiveness.
Benefits of Lightweight Insulating Concrete
Lightweight insulating concrete (LWIC) offers numerous benefits that make it a preferred choice in construction projects aiming for energy efficiency, structural integrity, and sustainability. This article explores the advantages of lightweight insulating concrete in detail, highlighting its key benefits across various applications.
1. Thermal Insulation
One of the primary benefits of LWIC is its exceptional thermal insulation properties. The incorporation of lightweight aggregates such as perlite, vermiculite, or foam creates air voids within the concrete, which significantly reduces heat transfer through building structures.
This thermal resistance helps maintain comfortable indoor temperatures year-round, reducing the need for excessive heating or cooling and contributing to energy savings.
- Reduced Energy Consumption
- Enhanced Comfort in Buildings
- Compliance with Energy Codes and Standards
2. Weight Reduction
Compared to traditional concrete, LWIC is significantly lighter in weight. This characteristic makes it easier to handle and transport during construction, reducing labor costs and equipment requirements.
The lighter weight also minimizes structural loads on buildings, allowing for more flexible design options and potentially reducing the need for additional support structures.
- Ease of Installation
- Improved Structural Efficiency
- Suitable for Roofing and Elevated Floors
3. Fire Resistance
Certain types of lightweight insulating concrete, such as perlite and vermiculite concrete, exhibit excellent fire-resistant properties. These materials do not combust easily and can withstand high temperatures, making them suitable for fire-rated assemblies in buildings.
LWIC contributes to enhancing overall fire safety measures and may help in meeting regulatory requirements for fire protection in construction.
- Fire-Rated Construction
- Protection of Structural Elements
- Insurance Benefits
4. Sound Insulation
The porous nature of LWIC materials contributes to effective sound absorption and insulation. This makes it a valuable choice for applications where noise reduction is essential, such as in multi-family housing, commercial buildings, and educational institutions.
LWIC helps create quieter indoor environments by reducing airborne noise transmission between rooms and floors.
- Acoustic Comfort
- Privacy Enhancement
- Compliance with Soundproofing Regulations
5. Environmental Sustainability
Many lightweight insulating concrete formulations utilize recycled materials as aggregates, reducing the environmental impact associated with concrete production.
Additionally, the energy-saving benefits of thermal insulation contribute to overall building efficiency and sustainability. LWIC supports green building initiatives by improving energy performance ratings and reducing carbon footprints.
- Use of Recycled Materials
- Energy Efficiency Benefits
- LEED and Green Building Certifications
Applications of Lightweight Insulating Concrete
Lightweight insulating concrete (LWIC) finds versatile applications across various sectors of the construction industry due to its unique properties of thermal insulation, reduced weight, and structural efficiency. This article explores the diverse applications of lightweight insulating concrete, highlighting its benefits and suitability for different types of projects.
1. Roofing Systems
LWIC is widely used as an insulating layer in roofing systems. Its lightweight nature reduces structural loads on buildings while providing excellent thermal insulation. Roof decks made of lightweight, insulating concrete help regulate indoor temperatures and enhance energy efficiency in residential, commercial, and industrial buildings.
- Flat Roof Insulation
- Pitched Roof Insulation
- Green Roof Installations
2. Floor Insulation
In flooring applications, LWIC serves as a lightweight and efficient insulation material. It can be poured over existing floors or directly onto subfloors to improve thermal comfort and reduce heat loss. Lightweight insulating concrete is particularly beneficial in radiant floor heating systems, ensuring even distribution of heat and energy efficiency.
- Underfloor Heating Systems
- Soundproofing in Floors
- Lightweight Fill for Raised Floors
3. Void Filling
LWIC is used for filling voids and cavities in construction projects. Its flowable nature allows it to conform to irregular shapes and spaces, making it ideal for filling around pipes, utility trenches, and beneath slabs. Lightweight insulating concrete helps stabilize the ground and prevent settling in areas where traditional fill materials may be impractical.
- Pipeline Trench Backfill
- Underground Utilities
- Bridge Approach Void Filling
4. Road Construction
In road and pavement construction, LWIC is utilized for its lightweight properties and ability to reduce pavement thickness. It serves as a base or subbase material that enhances pavement insulation, reduces frost susceptibility, and minimizes thermal stresses. Lightweight insulating concrete improves the longevity and performance of roads in various climates.
- Subbase Material
- Thermal Insulation in Roads
- Lightweight Fill in Road Construction
5. Insulating Concrete Blocks
Lightweight insulating concrete blocks are used in masonry applications to construct walls with enhanced thermal insulation properties.
These blocks are easy to handle and install, offering both structural support and energy efficiency benefits. Insulating concrete blocks contributes to sustainable building practices by reducing energy consumption and improving indoor comfort levels.
- Exterior Wall Construction
- Partition Walls
- Fire-rated Wall Assemblies
How Lightweight Insulating Concrete is Made
Understanding the manufacturing process of lightweight insulating concrete (LWIC) is crucial for construction professionals and enthusiasts alike. This article delves into the methods and ingredients used to produce LWIC, highlighting its composition, mixing techniques, and curing processes.
1. Ingredients
Lightweight insulating concrete typically consists of a blend of cementitious materials, lightweight aggregates, water, and additives. The choice of ingredients varies depending on the desired properties of the concrete. Common lightweight aggregates include:
- Perlite
- Vermiculite
- Expanded clay or shale
- Foam agents or air-entraining admixtures
2. Mixing Process
The mixing process is critical in achieving the desired consistency and properties of LWIC. It involves thoroughly blending the cementitious materials, lightweight aggregates, and water to form a homogenous mixture. Depending on the application and specific requirements, additives such as plasticizers or accelerators may be incorporated to enhance workability or accelerate curing.
- Batch Mixing vs. Continuous Mixing
- Proportioning of Materials
- Mixing Time and Techniques
3. Pumping and Placement
Once mixed, lightweight insulating concrete is typically pumped into place using specialized equipment. This method ensures uniform distribution and efficient placement of the material, especially in areas with limited access or complex geometries. LWIC can be poured directly onto substrates or into formwork, depending on the construction requirements.
- Pumping Equipment
- Flowability and Workability
- Placement Techniques
4. Curing
Curing is a critical step in the production of LWIC, where the concrete is allowed to harden and develop its strength over time. Proper curing conditions, such as temperature and humidity control, ensure optimal hydration of the cementitious materials and enhance the durability of the finished product. Curing times may vary depending on factors such as ambient conditions and the specific composition of the concrete mix.
- Curing Methods (Moist Curing, Steam Curing, etc.)
- Duration of Curing
- Quality Control and Inspection
Characteristics of Lightweight Insulating Concrete
Lightweight insulating concrete (LWIC) possesses distinct characteristics that distinguish it from traditional concrete, making it a preferred choice in modern construction projects. This article explores the key characteristics of LWIC, highlighting its properties, benefits, and applications across various sectors.
1. Low Density
One of the defining characteristics of LWIC is its low density compared to conventional concrete. This is achieved by incorporating lightweight aggregates such as perlite, vermiculite, or expanded shale into the concrete mix. The low density not only reduces the overall weight of the structure but also improves thermal insulation properties.
- Benefits of Low Density
- Structural Implications
- Impact on Construction Efficiency
2. Excellent Thermal Insulation
LWIC is renowned for its superior thermal insulation capabilities. The incorporation of lightweight aggregates creates air voids within the concrete, which act as barriers to heat transfer. This property helps maintain consistent indoor temperatures, reduces energy consumption for heating and cooling, and enhances overall occupant comfort.
- Thermal Conductivity
- Energy Efficiency Benefits
- Compliance with Building Codes
3. Fire Resistance
Certain types of lightweight insulating concrete, particularly those containing perlite or vermiculite aggregates, exhibit excellent fire-resistant properties. These materials do not easily combust and can withstand high temperatures, making them suitable for fire-rated assemblies in buildings. LWIC contributes to improving fire safety measures and may help in achieving regulatory compliance.
- Fire Rating Classifications
- Applications in Fire Protection
- Safety Benefits
4. Sound Absorption
The porous structure of LWIC contributes to effective sound absorption and noise reduction within buildings. This makes it ideal for applications where acoustic comfort is essential, such as residential units, offices, schools, and healthcare facilities. LWIC helps minimize airborne noise transmission between rooms and floors, enhancing overall indoor acoustic quality.
- Acoustic Performance Metrics
- Applications in Soundproofing
- Impact on Building Occupancy
5. Durability and Strength
Despite its lightweight nature, LWIC maintains adequate structural integrity and durability. The combination of cementitious binders and lightweight aggregates ensures robust performance under varying environmental conditions. LWIC is designed to withstand compressive forces, moisture exposure, and other external factors, ensuring long-term reliability in building constructions.
- Strength Characteristics
- Longevity and Maintenance
- Resistance to Environmental Factors